【第5章】第3節 災害事例②
3-2 災害事例:酸素欠乏
1 化学装置
窒素が封入されている配管内に点検に入った作業者が酸素欠乏症(機械器具設置工事業:休業1名)
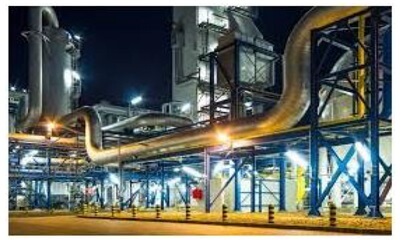
(1)発生状況
① 化学装置の定期修理工事を受注し、下請けが作業を実施した。
② 工事は、EDC(エチレンジグロライド)製造設備の開放検査と循環配管(直径50cm)に短管を取付けるもので、製造設備の内部は前日に窒素パージ(窒素封入)が行われていた。短管はあらかじめ元請の工場で製作されたものを、EDC循環配管に幅32cmの切り込み口を作り、そこにフランジを設けて取付ける計画であった。
③ 被災者は循環配管の工事にあたって、先に行った開放検査において循環配管内に工具やボルト等の置忘れがないかを確認するために、配管内に立ち入った。
④ 配管内に立ち入る前に、循環配管内の切り込み口から150cmの位置で酸素濃度を測定したところ、18%以上であったので、窒素はすでに放出されていると判断し、ハロゲンガス用の防毒マスクとゴーグルを着床し、循環配管内に這うように進入した。その後約3分経過頃、配管内で気を失い倒れた。
(2)原因
① 配管内の酸素濃度測定手順が不適切であった。
② 酸素欠乏状態の配管内に立ち入った。
③ 送気マスクを使用せず、ハロゲンガス用防毒マスクを使用した。
④ 循環配管内の残留物を確認するにあたり、事前打ち合わせが行われなかった。
⑤ 酸素欠乏危険作業に係る危険性の意識が不十分であった。
⑥ 元請と請負者(作業担当者)の連絡体制が不十分であった。
⑦ 元請が請負者に対して安全衛生指導を行っていなかった。
⑧ 化学設備内部に際し、酸素欠乏危険作業が予想されるにも関わらず、その準備がなされていなかった。
(3)再発防止対策
① 窒素パージした配管内部に立ち入る際は、十分換気し、適切な位置と方法で酸素濃度を測定し、安全を確認するとともに、作業時には監視人を配置し、空気呼吸器又は送気マスクを着用して作業を行う。
② 適切な作業手順を策定し、これにより作業を行う。
③ マニュアル等を作成し、不安全な状態及び不安全な行動がないよう指導監督を行う。
④ 残留物の確認はファイバースコープ等を用いて外部から実施できるようにする。
⑤ 工具・部品類は、事前にリストを作成し、作業開始前及び終了後に作業箇所への残留物を確認できる体制を整える。
⑥ 元請は、下請け業者の作業方法について指導監督等統括管理を徹底する。
⑦ 安全衛生管理体制を充実する。
⑧ 安全衛生教育を徹底する。
2 液体窒素
液体窒素が充満している保冷車の荷台に入り、荷降ろし作業中の酸素欠乏症(運輸交通業:休業1名)
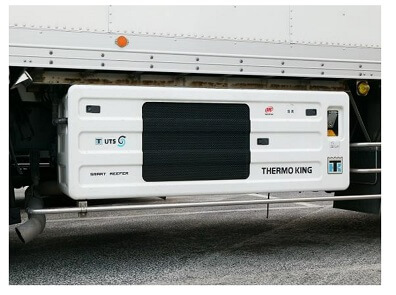
(1)発生状況
① 保冷車の冷凍設備は、液化窒素式低温輸送装置であり、トラックのシャーシーの下部に液体窒素容器が取付けられており、その容器の電磁弁の開閉作動により冷凍庫内天井部に取付けられたスプレーヘッダーから液体窒素が噴出し、庫内を冷凍する構造となっている。
② 本件に使用した保冷車には、冷凍庫内に噴出された液体窒素を外部へ排出する装置はなく、当日の荷降し作業では、作業開始前に冷凍庫の扉を5分程度開放し、窒素を放出していた。
③ 災害が発生した当日は、早朝に被災者が出勤したところ、荷降し作業予定の保冷車はすでに到着しており、運転者はエンジンをかけたまま運転席で仮眠していた。
④ 被災者は、いつものように扉近くにある荷を降ろそうとして窒素が噴出されている状態の冷凍庫の扉を開けて、1.5mの高さを這い上がり、庫内の冷凍食品を降ろしている間に窒素ガスを吸入して酸素欠乏症に罹った。
(2)原因
① 窒素ガスが噴出されている冷凍庫内に立ち入ったため窒素ガスを吸入した。
② 保冷車の運転者が仮眠中であったため、窒素ガスの噴出を停止することができなかった。
③ 日ごろから、問題なく冷凍庫扉近くにある荷を降ろす作業を行っており、酸素欠乏の危険性に対する意識が希薄になっていた。
④ 酸素欠乏危険作業主任者が選任されていなかった。
⑤ 保冷車からの荷下ろし作業に関するマニュアル類が作成されていなかった。
⑥ 作業に関する適切な指示がなく、作業者は個々の判断で作業を行っていた。
⑦ 日ごろ行われている作業方法についての安全性の検討を行うための管理体制が不十分であり、繰り返される不安全行動が見過ごされ、危険に対する感覚が薄れていた。
(3)再発防止対策
① 冷凍庫内に入るときは、窒素ガスの噴出を停止し、扉を開けて庫内に充満した窒素ガスを排出し、庫内の酸素濃度が18%以上になったことを確認した後に庫内に入る。
② 冷凍庫内に充満している窒素ガスを排出するための換気装置を設ける。
③ 冷凍庫の扉を開けたとき、窒素ガスの噴出を停止し、換気装置が自動的に作動する機構を設ける。
④ 窒素など不活性ガスを使用する冷凍庫内に入るときは、酸素欠乏危険作業主任者を選任し、その者に作業方法の決定等冷凍庫内で酸素欠乏空気を吸入しないよう適切な作業を直接指揮させる。
⑤ 作業者に対して、酸素欠乏症の危険性及び防止対策についての教育を実施する。
⑥ 作業の安全性を検討する体制を確立し、危険作業についてのマニュアル類を整備する。
3 溶接
作業中に発生した酸素欠乏症(金属製品製造業:死亡1名)
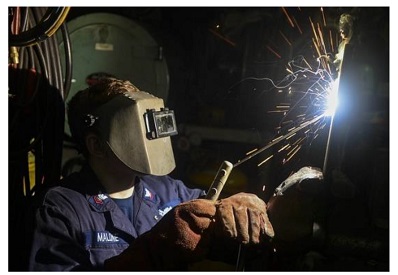
(1)発生状況
① 本作業には、溶接工である被災者をはじめ、パイプの取付け工2名、仕上げ工3名、電気計装工2名の計8名が従事しており、被災者は潤滑油貯蔵タンクに通じるパイプの溶接作業を1人で行っていた。
② 通常パイプどうしを溶接する場合、パイプ内の酸化を防ぐため、アルゴンガスを流して、パイプの外側からTIG溶接を行うことになっていた。
③ 災害当日、被災者は午前9時45分頃から、潤滑油貯蔵タンクに取付けるパイプの溶接作業を開始した。
④ 被災者は2インチのパイプを3箇所、4インチのパイプを1箇所溶接後した。さらに4インチのパイプを2箇所溶接するためタンク内に入ったところ充満したアルゴンガスにより酸素欠乏症となり死亡した。
(2)原因
① 通常、パイプの溶接作業では、酸化防止のためパイプ内をアルゴンガスで置換えする。この作業手順は、タンク頂部のフランジ部を外し、アルゴンガスを流した後、端を粘着テープで養生し閉止する。しかし、被災者は手間を省くため、フランジを外さずにパイプ内にアルゴンガスを流していた。その後、パイプ端部を粘着テープで閉止するために酸素欠乏状態のなっているタンク内に入った。
② 被災者が従事していた溶接作業は単独作業であり、作業手順や不安全行動を監視する者が配置されていなかった。
(3)再発防止策
① タンク内に通じるパイプ内部を不活性ガスで置換えする場合は、タンク内部へ不活性ガスが漏出しないように、パイプに閉止板を取付ける等安全対策を講じる。
② 酸素欠乏災害を防止するために作業手順を作成し、関係作業者に十分な教育を行う。
③ 複数の職種の作業者が混在している場合は、作業指揮者を指名し、作業手順沿って作業を直接指揮させる。
地域・講習・人数に合わせてすぐに予約可能
講習会を予約する受講者様のご希望に合わせ、以下のタイプの講習会もご用意しています




このページをシェアする
講習会をお探しですか?